Hoteliers Look to Modular Technology for Solutions to Speed & Quality Issues
FOLSOM, California – May 1, 2016 – Looking to solve the problem of building a quality product in a short amount of time, both Marriott International and Tharaldson Hospitality Management looked to modular technology and Guerdon for the solution. Long a leader and innovator, Tharaldson took the lead and was among the first to make Marriott’s modular initiative a reality.
The Folsom Marriott Fairfield Inn & Suites is a 97 room, 52-module, three-story hotel that was assembled on site in four short days during the month of April, 2016. With storm clouds on the horizon, crews from Guerdon and ProSet stacked and weather-proofed the last modules.
Protecting interior units from water infiltration is top priority for modular and onsite builders alike. What sets Guerdon apart is level of care when it comes to weather protection. At the factory, Guerdon’s team installs a 3/8” OSB and a fully adhered, 40-mil EPDM member at each ceiling and roof level. Prior to leaving the factory, each module is shrink-wrapped and inspected in preparation for shipping. Once on site, the modules are again inspected and prepped for staging. During the process of stacking, each module is carefully unsealed and readied for placement. Finally, once the modules have been stacked, the EPDM is joined, the roof joints sealed, the wall membrane lapped, and any exposed surfaced covered to prevent any water infiltration.
Folsom’s 52 modules were fabricated in a short six weeks period in Guerdon’s Boise, Idaho factory while Tharaldson crews prepared the site and placed the foundations and stem walls. Prior to shipping, FF&E (Furniture, Fixtures, and Equipment) was installed. In the case of a hotel project, the FF&E would include beds, sofas, chairs, desks, end tables, pictures, television sets, blinds, lights, and more. What was not physically installed was packed loose and tied down for shipping. Having the FF&E installed at the factory is not only convenient, it’s also a time and money saver. With the units fully furnished when the module arrives on site, crews spend less time in the suite and there is less interference of hotel staff training.
With a Fall 2016 opening, Tharaldson will begin collecting revenues six months earlier than had they gone with site built construction. Larry Madson, Tharaldson director of hotel construction, is pleased to be using modular technology to reduce his costs and help make his team more efficient and more responsive their customer’s needs.
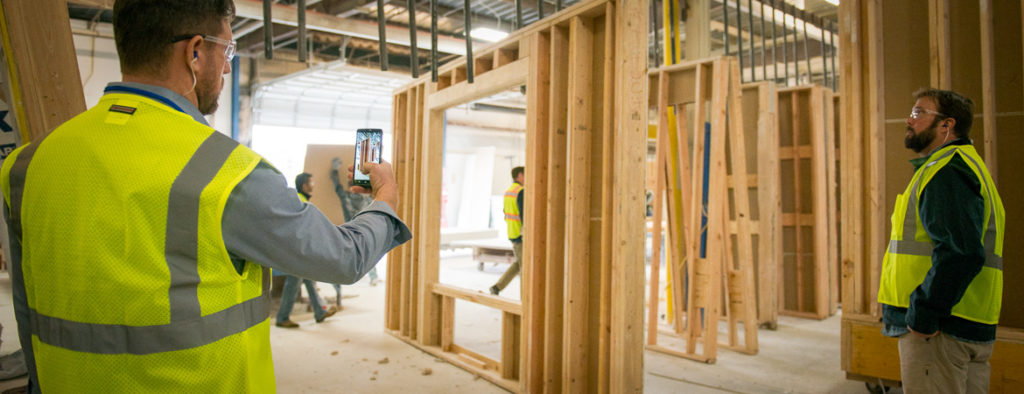
Contractors and Hotel Developers tour Guerdon’s Boise, Idaho factory to learn more about Modular Technology for Hotel Development.
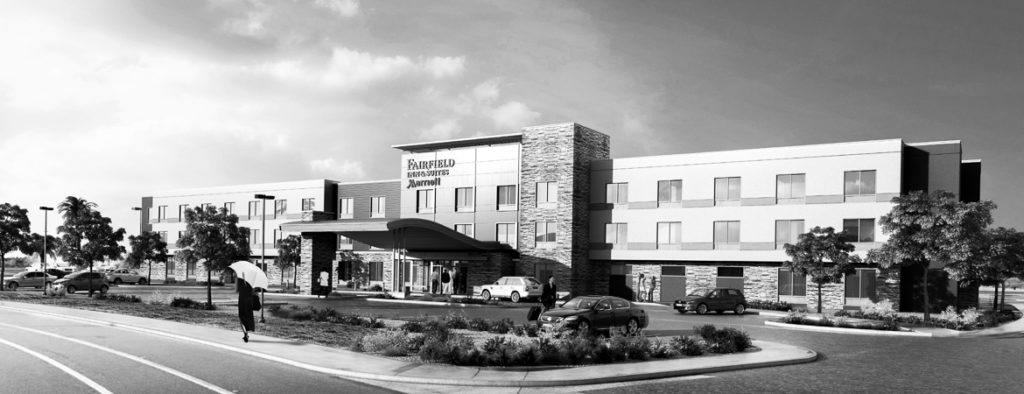
Rendering of the Folsom Fairfield Inn.
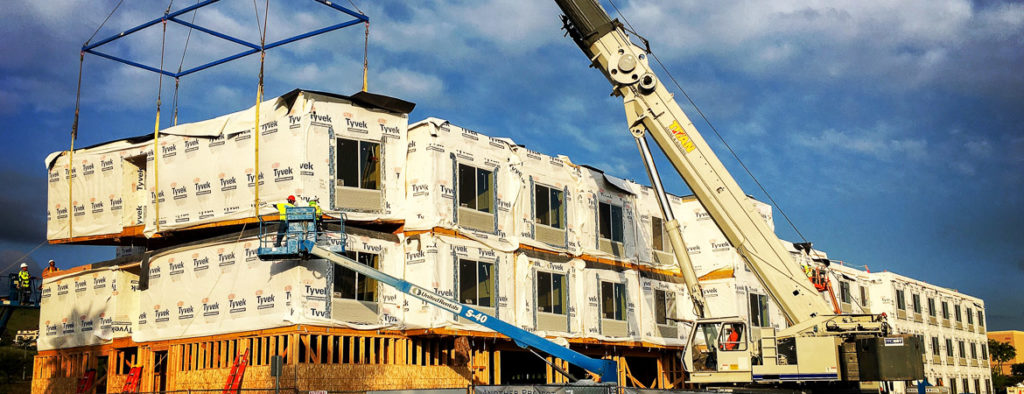
Final module being craned into place on the Folsom Fairfield Inn in Folsom, CA.
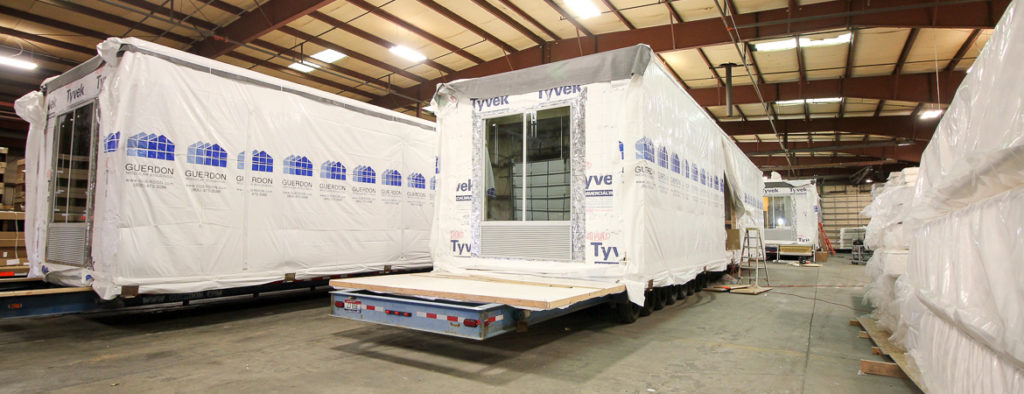
FF&E Factory Installation Photo of the Folsom Fairfield Inn project.